Resino supports the development of monoplast packaging
Plastic pollution is a big environmental concern, both on a local and a global scale.
Many plastic materials cannot be recycled because they consist of several materials of plastic which are very difficult to separate. When thrown out, the packaging of these plastic materials is burned instead of being recycled.
This creates a need for developing packaging consisting of one plastic material. Therefore, Resino Inks has joined the Circular Monoplast Packaging Project.
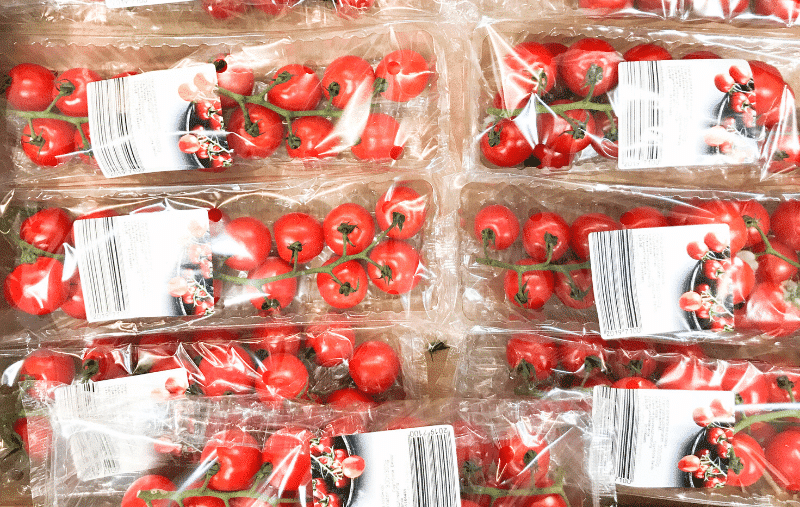
New EU directive on packaging waste
It will be costly for companies if they do not find a solution that enables packaging to be recycled. In 2025, a new EU directive will come into force stating that producer responsibility schemes shall be established for all packaging. This means that producers will have to pay for the used plastic in their products to be recycled.
Multilaminate film may be wasted
Approximately 50% of a household’s plastic waste consists of flexible film, for instance from food packaging. Half of the flexible film is multilaminate film, meaning the film contains mixed plastic materials.
Process of multilaminate film when thrown out
For example, the cheese you buy from the supermarket is most likely packed in a multilaminate film.
However, this makes it much more difficult to recycle the packaging into new products, after the cheese is consumed.
When the cheese’s packaging is thrown out in the plastic container, the plastic packaging is collected. Afterwards, the plastic will be sent to a place where the plastic is chopped into tiny pieces.
Advantage of monoplast packaging
If the packaging only consists of one plastic product, it is more likely that these tiny pieces can be recycled into a new product.
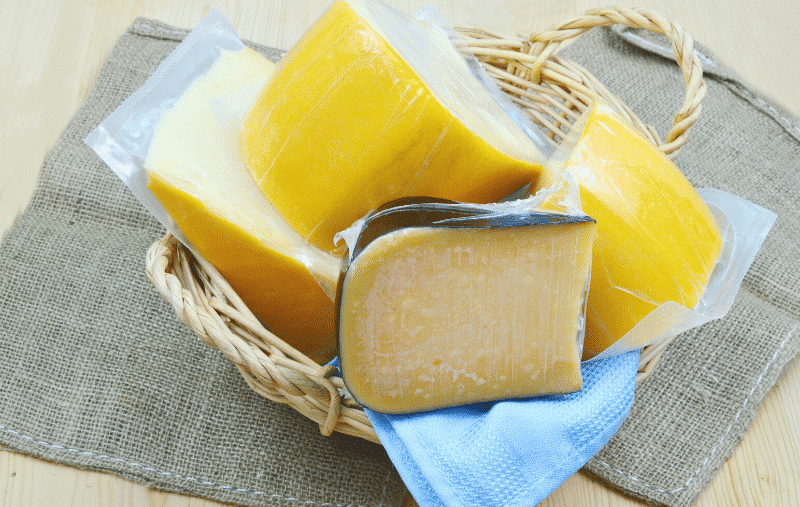
Project Circular Monoplast Packaging
In the project Circular Monoplast Packaging, the goal is to develop a mono material of polyester for packaging that can be recycled.
In this way, much less packaging waste needs to be burned, and these solutions will give companies a competitive advantage when the EU directive takes effect in 2025.
Monoplast packaging of one polyester material
Today, the plastic materials, polyethylene and polypropylene, are often printed on plastic packaging.
However, when using multiple plastic products it is much more difficult to recycle the packaging, since it will contain mixed plastic materials.
Thus, this project will focus on developing monoplast packaging made of only polyester.
About this project
Resino Inks has joined the project together with several companies and helps develop solutions. The Innovation Fund Denmark has invested DKK 11 million in this project. Circular Monoplast Packaging is a three-year project and started in May 2020.
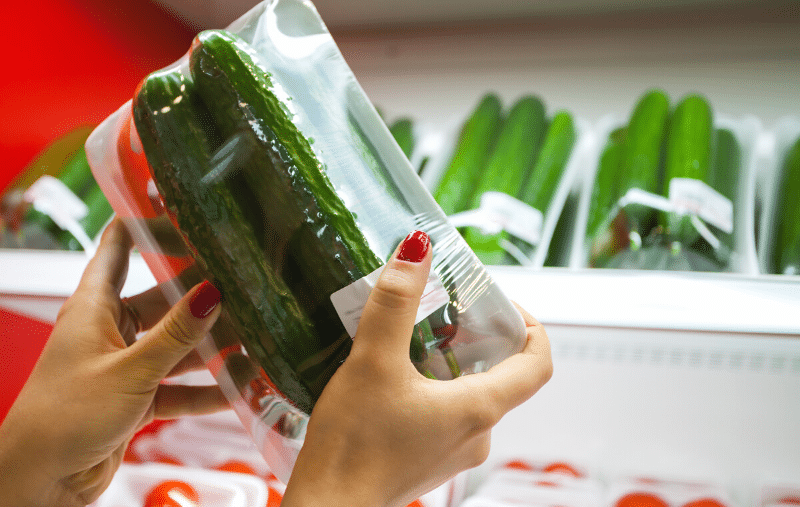
Resino’s role in the monoplast project
In the Circular Monoplast Packaging project, four key technologies will be developed in close cooperation with the joined companies.
Resino is contributing to the technology making mono PET film weldable on ordinary packaging lines.
Heat-seal lacquer
In most food packaging companies, heat-sealing temperatures are below 190°C. Therefore, it is a challenge that the material of mono PET film has a high melting point – more than 200°C.
This means that a heat-seal lacquer must be applied that does not contaminate the circular flow of PET. Therefore, it is necessary to develop a heat-seal lacquer which Resino is committed to.
Heat-sealable particles in lacquer
Resino has developed a heat-seal lacquer which can contain heat-sealable particles. The idea is that the heat-seal lacquer goes together with polyester particles which are dispersed into the heat-seal lacquer.
When the heat-seal lacquer is heated together with the particles, the lacquer gives a good heat-seal strength.
Heat-seal lacquer used by printing companies
The solution will be used by printing companies that print the heat-seal lacquer on the mono PET film.
A thin layer of this heat-seal lacquer is applied exactly where the film is to be heat-sealed. This ensures that the film can be recycled when it ends up as waste.
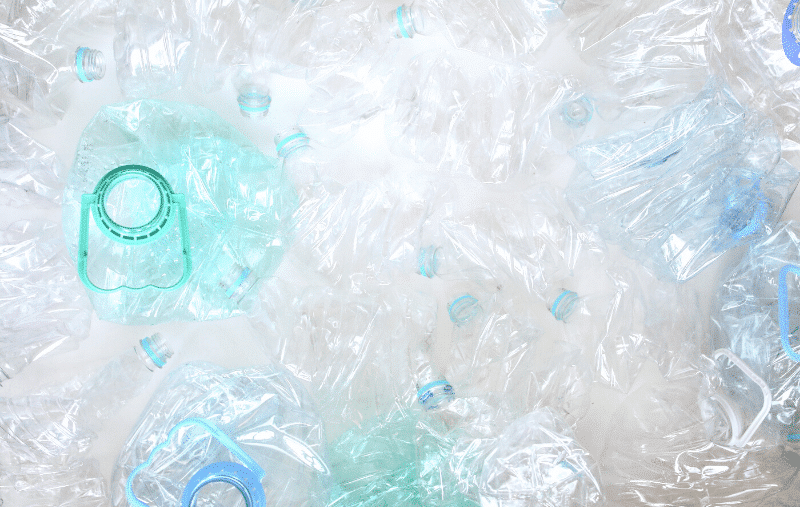